Is your process safe from exothermic effect?
- May 5, 2022
- Posted by: veeyor@dmin
- Category: Epoxy resins
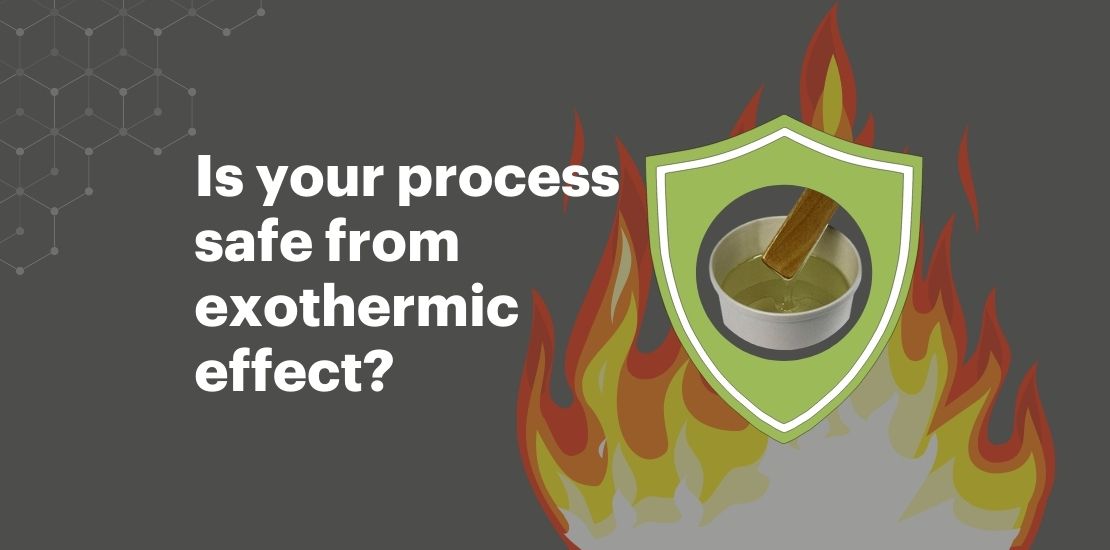
Epoxy resins are comprised of a mixture of resin and hardener. Proper mixing of the two components is important not only for the quality and reliability of the end product but also from the safety point of view. A considerable amount of heat is generated when the epoxy resin cures. This phenomenon is known as the exothermic effect
How exothermic effect affects process safety?
During the curing process, the epoxy and the hardener undergo thermal decomposition. This process makes the resin frothy and generates considerable heat and toxic vapors. Gasses generated during this process include ammonia, nitrogen oxides, aldehydes, and even carbon monoxide.
Fans can be used to drive the fumes away from the humans, however, proper ventilation in the mixing and curing area is a must.
If the epoxy resin is left to cure in a contained mass such as a mixing pot, the curing process can generate enough heat to melt the plastic. The thicker the epoxy mass, the more heat will be generated.If the combination of epoxy resin and filler is wrong, it could generate enough heat to smolder and start burning.
100 grams of mixed epoxy resin could easily reach up to 400degrees Centigrade. Such high temperatures even up the risk of fire.
What can be done to control the exothermic effect?
Choose the epoxies that cure slowly
Epoxy resins can be customized to achieve a desired speed of cure. However, do note that a faster curing process will generate more heat. On the other hand, a slower curing rate also slows up the heat buildup. Additionally, a slower rate of curing allows deeper pouring before more heat is built up.
Veeyor Polymers works closely with the clients to study their application requirements and suggest a suitable epoxy resin mix. Backed by 30 years of experience, Veeyor has developed a deep R&D expertise in developing customized resins, including safer and non-flammable resins.
Introduce heat sinks
Heat sinks are objects that will absorb the heat of the resin and keep it cooler. For instance, if the resin is being applied on metal surfaces, the metal absorbs most of the heat. On the same note, fillers with a higher density also absorb more heat and take up more volume than low-density fillers. The low-density fillers also discourage heat, but they act more like insulators than heat-absorbers.
Keep the temperature cool
Maintaining a cooler temperature on the shop floor will aid in cooling the epoxy faster. Additionally, if the epoxy itself is cooled sufficiently before pouring, it could allow you to pour deeper before a serious heat build-up.
Pour the resin in batches
If there is a mild exothermic effect noticed in the resin being poured, you could wait for the resin to cool a bit before pouring the next round. Timing the pouring batches right is critical when undertaking multiple pours. A shorter than required interval between pouring rounds leads to more heat generation. Similarly, too long an interval could lead to insufficient bonding.
Conclusion
MIxing and curing of epoxy resins has long-term implications for process safety. The amount of epoxy being mixed and poured should be considered carefully to control the exothermic effect. Consulting with your resin partner on the right ways to mix and pour epoxy resin could help ensure a smarter and safer process.